Plastic extrusion for economical product fabrication
Plastic extrusion for economical product fabrication
Blog Article
Understanding the Fundamentals and Applications of Plastic Extrusion in Modern Manufacturing
In the realm of modern-day production, the strategy of plastic extrusion plays an important duty. Unwinding the principles of this procedure discloses the real adaptability and possibility of plastic extrusion.
The Fundamentals of Plastic Extrusion Process
While it might appear complex, the principles of the plastic extrusion process are based on relatively straightforward principles. It is a production process in which plastic is melted and then shaped into a constant account with a die. The raw plastic product, commonly in the type of pellets, is fed right into an extruder. Inside the extruder, the plastic is subjected to heat and pressure, creating it to melt. The liquified plastic is after that compelled through a shaped opening, called a die, to form a long, constant product. The extruded item is cooled and after that cut to the wanted size. The plastic extrusion procedure is thoroughly utilized in different industries as a result of its cost-effectiveness, versatility, and performance.
Various Kinds Of Plastic Extrusion Techniques
Building upon the basic understanding of the plastic extrusion process, it is required to explore the numerous strategies involved in this production method. In comparison, sheet extrusion produces large, level sheets of plastic, which are usually further refined into items such as food product packaging, shower drapes, and cars and truck parts. Understanding these strategies is crucial to utilizing plastic extrusion successfully in contemporary manufacturing.
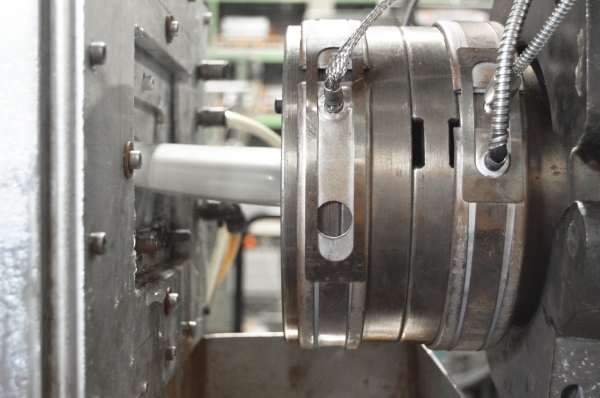
The Function of Plastic Extrusion in the Automotive Sector
An overwhelming majority of components in contemporary vehicles are items of the plastic extrusion process. Plastic extrusion is primarily made use of in the manufacturing of different automobile parts such as bumpers, grills, door panels, and dashboard trim. Hence, plastic extrusion plays a critical duty in automobile production.

Applications of Plastic Extrusion in Consumer Item Manufacturing
Past its significant impact on the auto market, plastic extrusion confirms just as efficient in the world of customer goods making. The convenience of plastic extrusion allows manufacturers to develop and produce complicated forms and sizes with high accuracy and efficiency. The versatility, adaptability, and cost-effectiveness of plastic extrusion make it a preferred option for several consumer goods makers, adding significantly to the market's growth and development.
Environmental Effect and Sustainability in Plastic Extrusion
The pervasive usage of plastic extrusion in manufacturing welcomes examination of its environmental effects. Efficient machinery minimizes power use, while waste monitoring systems reuse scrap plastic, reducing raw product demands. In spite of these renovations, even more development is required to mitigate the environmental footprint of plastic extrusion.
Final thought
In final thought, plastic extrusion plays an essential function in modern-day manufacturing, my response specifically in the auto and consumer goods fields. Understanding the basics of this procedure is key to maximizing its benefits and applications.
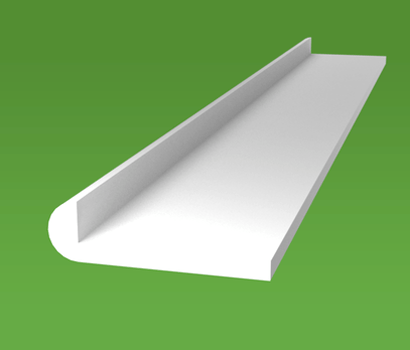
The plastic extrusion procedure is extensively used in numerous industries due to its effectiveness, versatility, and cost-effectiveness.
Structure upon the standard understanding of the plastic extrusion procedure, it is essential to explore the different techniques included in this manufacturing approach. plastic extrusion. In contrast, sheet extrusion produces large, level sheets of go to this website plastic, which are commonly further processed right into items such as food product packaging, shower drapes, and automobile Learn More parts.A frustrating majority of parts in modern vehicles are products of the plastic extrusion process
Report this page